What the Shock Testing Process Involves
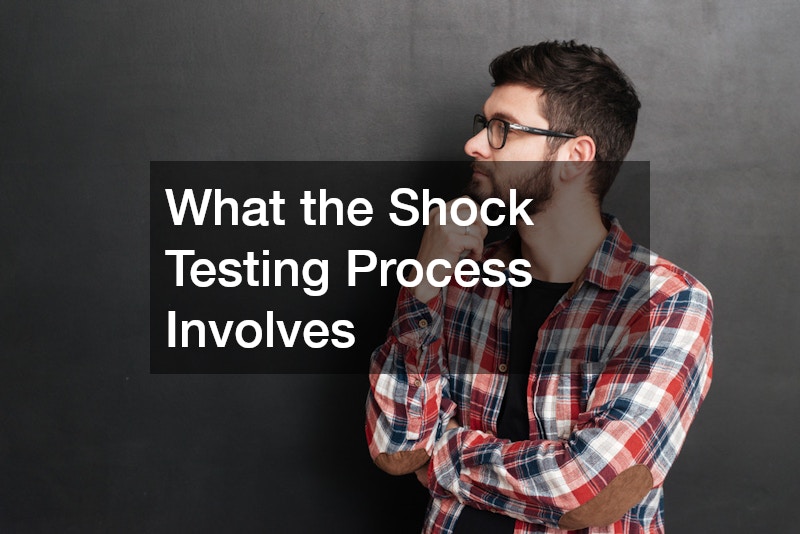
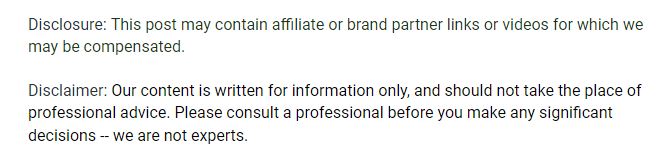
Shock testing is an essential process in evaluating how products withstand sudden impacts, vibrations, and forces during their operational lifecycle. This type of testing simulates the real-world conditions a product might experience during transportation, installation, or everyday use, ensuring that it can handle these situations without failure.
The shock testing process typically begins with the product being mounted on a test rig or fixture. Specialized equipment, like drop tables or pneumatic hammers, is used to deliver precise shocks at varying intensities. These shocks can be customized to replicate different scenarios, such as drops, collisions, or sudden stops.
During the test, sensors monitor how the product responds to the applied force, collecting data on factors like stress points, deformation, and overall resilience. This information is critical in assessing the durability of the product and identifying any potential design weaknesses. This data allows engineers to make informed decisions about material selection and structural integrity while helping determine whether the product meets industry-specific safety regulations and quality standards.
Manufacturers across various industries, from automotive to electronics, rely on shock testing to guarantee the long-term reliability of their products. By simulating extreme conditions, this process helps engineers make necessary design improvements and ensure that their products meet safety and performance standards.
.